Don’t let tool hoarding slow down your business.
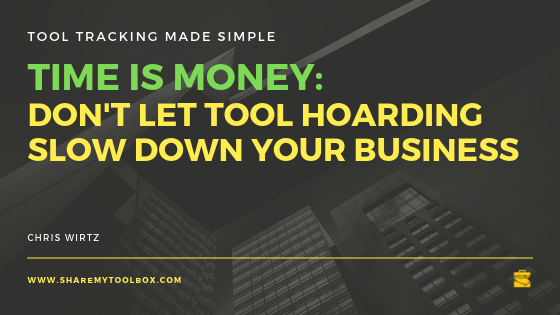
The two most important assets on any jobsite are your people and your tools. If either of these aren’t available, or aren’t being used effectively, you’re wasting money.
Tremendous effort usually goes into managing the labor on a job but often much less focus is spent managing small tools and equipment. If tools aren’t where they need to be, the costs begin to grow as labor time is wasted waiting or trying to locate the needed tools. Too often, the remedy to avoid not having a specific tool is “hoarding” them just in case they’re needed. This of course results in higher costs and more company-wide time wasting. Tool hoarding is a common occurrence in construction, but fortunately it can be remedied.
Can you relate?
Does the following scenario sound familiar? One of your projects has some important tools on site, so the tool manager holds on to them, arguing that they’re being used when actually they’re not. And since, in most cases, there’s no penalty for having unused tools on site, there’s no reason not to hoard! These tools end up sitting idle on the job site for days, weeks or months – un-billed and unaccounted for.
Tool Hoarding Effects Everyone
The old saying, “time is money,” is truer than ever when considering the time wasted by tool hoarding, as superintendents spend endless hours hiding and protecting their tools. Meanwhile, the warehouse manager wastes valuable time chasing tools down and trying to determine who’s using – or hiding them. According to Modern Contractor Solutions, “More than $1 billion in valuable tools, commodities, and consumables are lost each year.” And to be clear, the definition of “lost” also includes tools that are secretly held and hidden on a jobsite (hoarded), causing a company to repurchase tools that aren’t truly lost.
Unfortunately, many companies deal with tool hoarding by trying to use accounting policies to get superintendents and project managers to “cough up the tools” and return them. This rarely works. In the end it is much more efficient to provide everyone with visibility to who has the tools and where those tools are located. This insight to where the tools can be found opens up dialogue between superintendents who begin simply asking for what they need.
When superintendents talk directly, tools wind up where they’re needed and are regularly moved from idle jobs to active jobs. In the simplest terms, policies that make it hard to request and deliver tools to jobs actually make it more likely that tools will get hoarded in order to avoid the work delays of not having a required tool. If tools move quickly from job to job, then superintendents don’t feel the need to hoard things “just in case” they might need them.
Don’t use an accounting policy to solve an operations problem
So, let’s look a little deeper at how construction companies use accounting policies to address what is truly an operations problem. A great deal of accounting time in construction is spent administering and managing expensive time sheets. This requires a major time investment for employees to track their time and even more time for accounting employees who process the time and likely corrections. In fact, in an article in the Washington Business Journal, the American Payroll Association (APA) says “it takes five to six minutes to add and audit just one employees’ time card and manual time card computation errors can cost 1 to 8 percent of a company’s payroll!”
Interestingly, charging labor hours to jobs and charging small tools to jobs is essentially the same. You’re really just creating time sheets for tools! There’s a high organizational time cost of charging tools to jobs and this practice requires construction accountants to spend hours behind a desk connecting tool costing transactions to jobs, arguing with superintendents and changing transactions to correct inevitable mistakes.
Think about time sheets for tools this way – usage time has to be collected, then charged to jobs with mistakes corrected during and after processing. There is time required from superintendents plus time from office personnel to process, and then finally, time from management to review. But unlike payroll, this small tool time is a minor cost to the job and was truly only designed as a band-aid solution to reduce tool hoarding – which it fails miserably at doing!
If tool hoarding can be eliminated in a different, more efficient way, then tools can simply be costed to jobs as an automated allocation and all the costs to collect and process tool costs are eliminated. Let’s look at a better way of avoiding the pitfalls of tool hoarding.
It’s all about tracking
With tool hoarding disrupting the flow of construction operations, contractors are looking at new ways to manage their tool inventories. Having tried the “spreadsheet method,” contractors are now investing in small tool management systems. The most effective of these can be deployed easily as an “app” on team smartphones and tablets.
In an article published in Construction Business Owner, the author confirms this saying, “An automated tool control system can reduce the burden of labor shortages by allowing you to run a tool room with fewer staff and save money by not having to replace lost or stolen tools nearly as often.” He continues by declaring, “The ability to manage tool inventory remotely can significantly save construction companies time and money.” Put simply, tool tracking quickly gives you control over:
- Reduction in tool hoarding and equipment losses
- Tool control and inventory reconciliation
- Time saved during tool check-in and check-out
- Time saved by not searching for misplaced or lost tools
- Increased productivity because workers can find the right tool at the right time
After deploying a tool tracking solution, you’ll be able to assign tool responsibility to individuals and make it easy to transfer responsibility when a tool moves from person to person while giving everyone in your organization the ability to easily search for tools and see who has what.
By putting tool hoarding to rest at your organization, you’ll avoid wasted time searching for tools, eliminate the possibility of tools sitting idle, and most importantly – save you some real money.
If you’d like to learn more about modern tool tracking applications check out ShareMyToolbox, at https://www.sharemytoolbox.com or call, 866.768.8665
Learn more about modern tool tracking here. Also you can find numerous articles on tool tracking tips and contractor profiles of tool tracking success here.